Downtime Sucks
In the oil and gas industry, downtime caused by maintenance can have significant negative impacts on production. Pump jack maintenance is particularly critical due to its essential role in ensuring productive, safe, and compliant well sites.
This use case demonstrates how IronSight can assist your team to optimize pump jack maintenance and prevent issues before they happen.
Benefits for Demand
An oil and gas company’s primary goal is to maintain pump jacks efficiently and at a reasonable cost. They want to ensure that the right resources are assigned to the job, and that work is completed in a timely manner.
By implementing IronSight, oil and gas companies benefit from:
- Reduced failures and improved plan and processing availability.
- Getting more product to market
- Reduced cost by preventing failures that cost more time and money to repair compared to preventative efforts
- Better use of services and more efficient execution of planned activities
- Faster, more effective response for any unplanned emergency work
Benefits for Supply
A maintenance company's primary goal is to provide quality maintenance services for the oil and gas company. They want to ensure that any assigned resources are well utilized, and the work is completed efficiently.
Implementing IronSight helps maintenance service providers benefit from:
- Enhanced real-time monitoring of their maintenance crews
- Digital documentation to reduce paper-based administration
- Improved ability to plan and coordinate maintenance operations, as well as respond to emergency maintenance requests
- Increased quality, quantity, and velocity of maintenance-related data, so they can turn insights into efficiencies
All of these benefits help pump jack maintenance service providers increase utilization of their crews and equipment, streamline their administration, provide higher quality services, and ultimately make more money, with more clients.
How Pump Jack Maintenance is Typically Done Today
Many oil and gas companies have an ERP or CMMS to support the planning and documentation of maintenance activities.
While these solutions are great for managing maintenance from the office, most offer limited functionality when it comes to supporting maintenance in the field.
Most well-operators and maintenance providers still use paper forms and tickets, phone calls and texts, spreadsheets, and whiteboards to manage and coordinate the actual work that needs to be done. These traditional workflows can lead to a lag between what’s happened, what’s happening, and what still needs to get done.
Without accurate, up-to-date field insight operators and service providers alike can find themselves inadequately prepared for unforeseen circumstances and last-minute logistical challenges.
Challenges with Current Pump Jack Maintenance Approaches
As equipment ages or experiences excess strain brought on by process upsets and variance, failures become more common. More effort is required to keep production facilities and equipment working without downtime.
This can result in corrective maintenance dominating maintenance activities and draining resources and budgets. This often creates a compounding cycle that results in under-maintained equipment and poor performance.
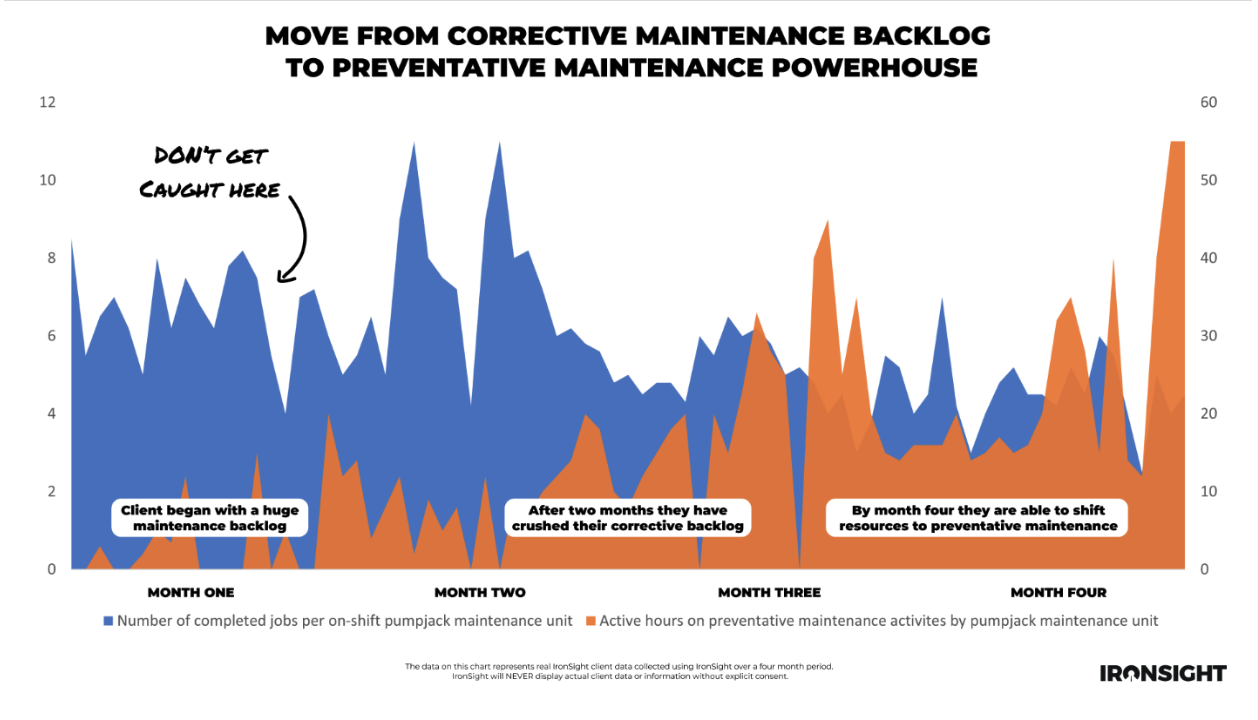
A lack of adequate documentation helps perpetuate these challenges because while your ERP/CMMS may be great at providing insight, these platforms need the right data to analyze – and that’s captured in the field, not in an office.
How Can IronSight Help?
So how exactly does IronSight help operators and service providers improve the effectiveness of their pump jack maintenance program?
IronSight can help maintenance management efforts by:
- Providing a simple, real-time scheduling platform
- Tracking maintenance activity including:
- Cost Centers
- Activity Type
- Job Forms
- Tool Time - Tracking failure codes
- Tracking bad actors (frequency of failures and pinpointing repeat problems)
- Tracking part failures (part manufacturer)
IronSight creates insight into the health of maintenance management by providing:
- Tracking planned vs unplanned maintenance activity measures
- Maintenance backlog tracking
By applying IronSight as your in-the-field pump jack maintenance solution, we’ll take your existing workflow and turn it into something similar to the workflow below. Every operator and service provider is unique, so your exact workflow with IronSight might look a little (or a lot) different in order to meet your needs.
Request
Maintenance requests, whether preventative (PMs) or corrective (CMs), usually originate from a CMMS or ERP. IronSight can seamlessly integrate with your planning systems to create a job or e-ticket that outlines the required maintenance tasks. Some clients choose to create these requests directly in IronSight.
Interested in creating maintenance requests in the field or office using IronSight?
Click here to learn more about IronSight’s Request features
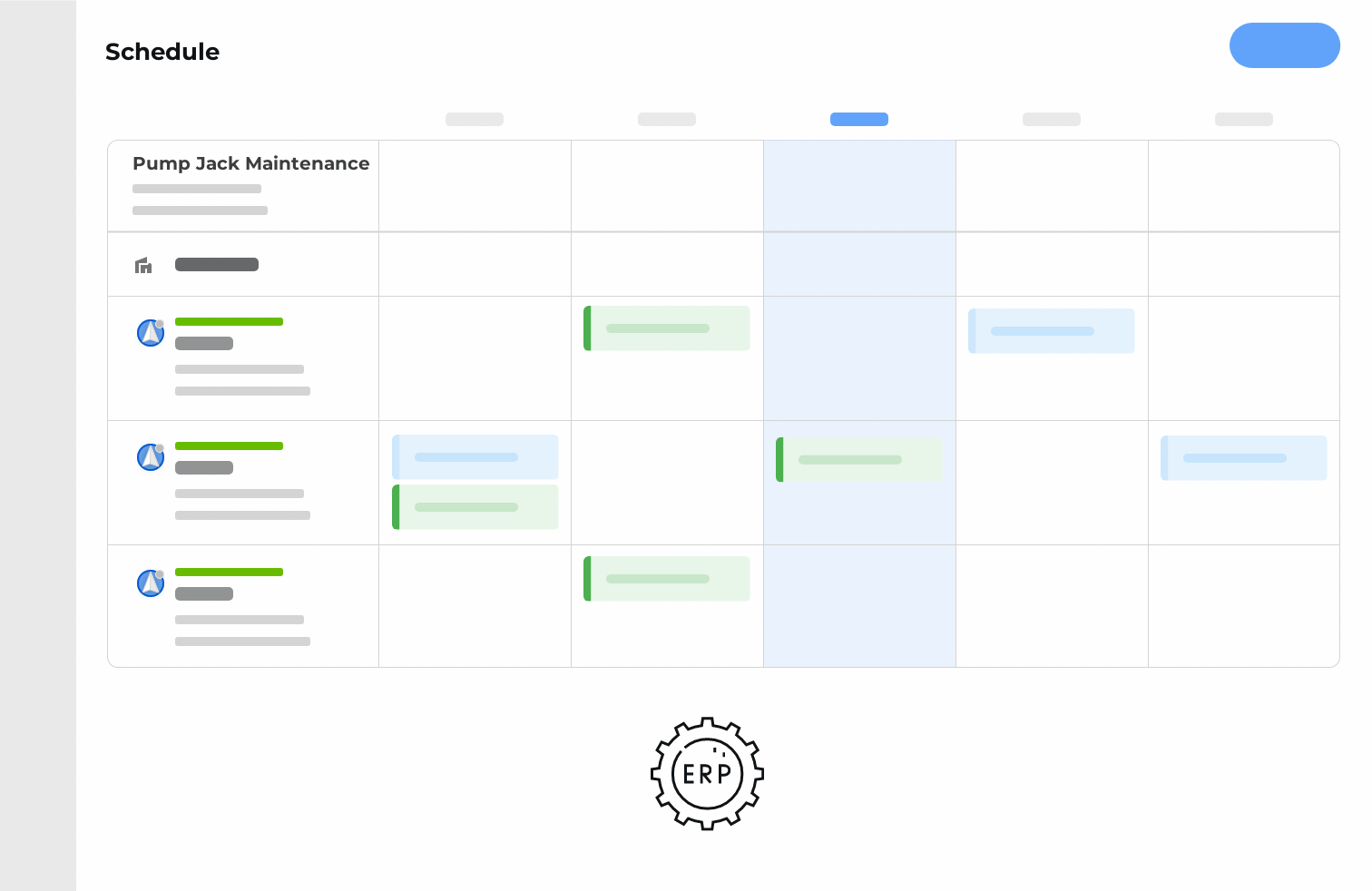
Schedule
After a maintenance job request is pulled into IronSight it goes to the preferred coordination team, ready to review and schedule. Some common workflows involve the coordinating team to be:
- The oil and gas company's command/dispatch center
- A 4PL provider's command center
- An IronSight Dispatch as a Service (DaaS) coordinator
- Sent directly to the service provider’s dispatch center
Using IronSight's web-based dispatch hub, the coordinator can easily assign the job to the optimal resource by accessing real-time information about the field. This improved visibility is especially helpful for scheduling CMs and jobs closer to the date and time of execution.
Click here to learn more about IronSight’s Schedule features
Execute
Once the job is assigned, maintenance crews simply log into the appropriate unit and instantly have a comprehensive list of work that they need to accomplish. As they complete their work, they’ll simply keep pressing IronSight’s signature big blue button to progress through each stage of the job.
Field teams benefit from:
- Detailed work lists
- Notifications for job updates
- Direct chat with the coordinator and other field crews
- Driving directions
- Elimination of paperwork
Click here to learn more about IronSight’s Execute features
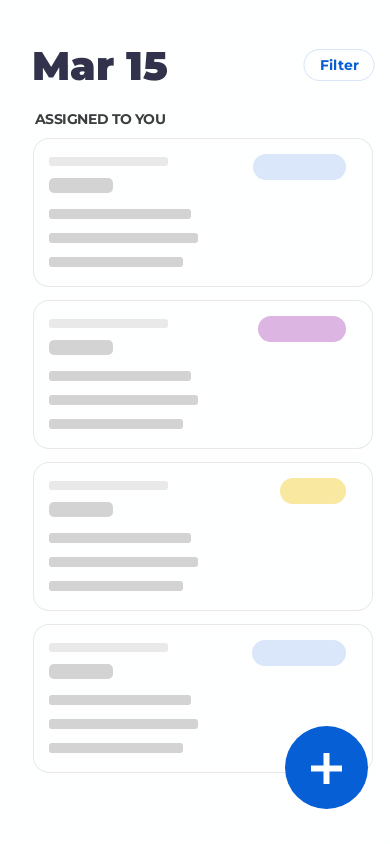
Document
IronSight's documentation step is crucial for pump jack maintenance, ensuring that all tasks are documented in detail.
Documentation works in three ways:
- Passive Documentation
- Automatically capture data such as location, travel distance, and time, cost centers and more - Job Documentation
- Allows field workers to document each step of their job using
customizable fields - Form Documentation
- Digital forms that can be tailored to specific job requirements.
With IronSight, you can capture all the necessary information, including new data that was previously unavailable.
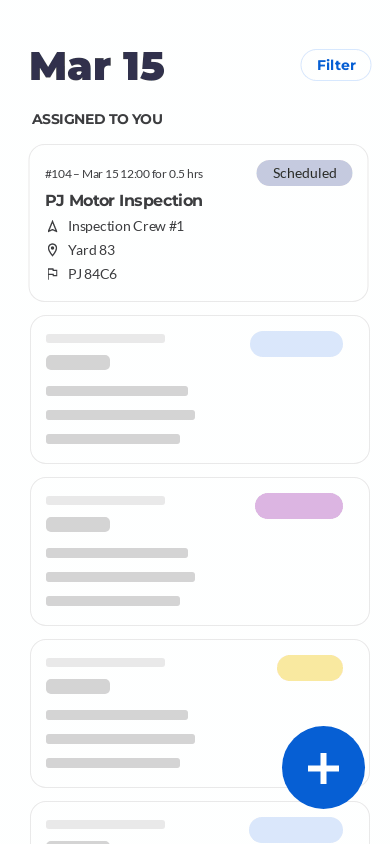
Click here to learn more about IronSight’s Document features
Approvals and Follow ups
Once a job and all the appropriate documentation is completed, it’s ready for review. The approval workflow can be configured in a number of different ways, but the most common is to send back to the initial requesting system or coordinator for approval.
If a form requires a follow-up action, this can be sent back to the CMMS/ERP or just filtered back into the IronSight – either automatically or with whatever degree of review or human input and review you prefer.
Analyze
Because everything that happens on IronSight is captured digitally, you’ll have a wealth of data unlocked for you to perform analysis and gain insight into what’s happening in your business.
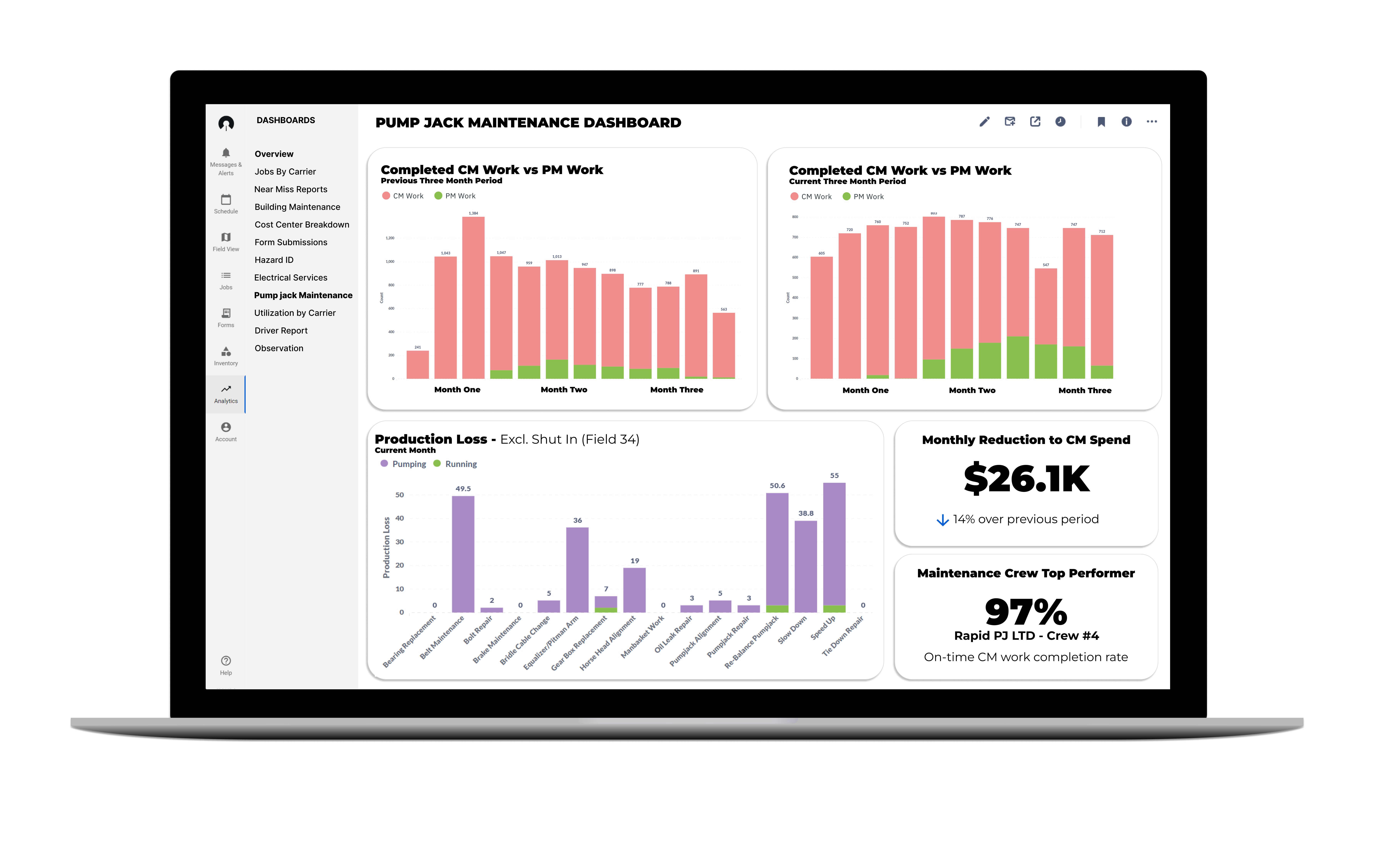
If you’re a well-operator, you may want to know things like:
- Damage code analytics
-Most common codes
-Damage codes by operating area - PM vs CM analytics
- Production loss
- Maintenance provider performance comparisons
If you’re a maintenance provider, you might be interested in:
- Most common damage codes by client
- Time to service breakdowns
- Maintenance tech comparisons
- Crew utilization metrics
- Safety analytics
Integrations Overview
As you might have guessed if you’ve made it this far, the most common type of integration for supporting a pump jack maintenance workflow would be connectingIronSight with your Computerized Maintenance Management System (CMMS), Enterprise Resource Planning (ERP) solution, Enterprise Asset Management system (EAM).
These types of software often allow for a direct integration that enables an automatic update of information between the system and IronSight.
Summary
Your exact maintenance plans, challenges, and goals will be unique to your operation. With that said, every oil and gas company and maintenance service provider can be confident that they will save time and money by digitalizing their field maintenance workflow.
Oil and gas companies can get more product to market, and maintenance providers can spend less money getting more work done.
To see how using IronSight for pump jack maintenance can support your goals, reach out today for a personalized walkthrough of IronSight for pump jack maintenance.