Fluid Hauling With IronSight
IronSight provides an end-to end platform to streamline fluid hauling.
We take gruntwork and guesswork out of fluid hauling for all companies and roles involved on the job:
THE DEMAND SIDE
- Rig consultants and well pad operators - request fluid to be delivered or loaded from field sites
- Fluid coordinators - schedule the job and decide which service providers or trucks should haul the fluid
THE SUPPLY SIDE
- Fluid haulers - haul fluid from A to B and collect additional field data
How are fluid volumes traditionally tracked?
Fluid haulers move production fluids from tanks on well pads to plants, disposal facilities, and sales terminals (or vice versa). They write-up paper trucking tickets that are the source of truth for fluid hauling data, and are the method by which trucking companies get paid (by the hour or by the volume hauled). Tickets need to be approved by the oil company with a stamp or signature. A copy is left at the pickup location, a copy is left at the destination, and a copy is kept by the driver as backup for invoice processes. The oil company collects thousands of these tickets every month and manually transfers the data into their production tracking software. Before IronSight became a technology company, we started out as an oilfield services provider called Pack Energy Services (see one of our tickets below).
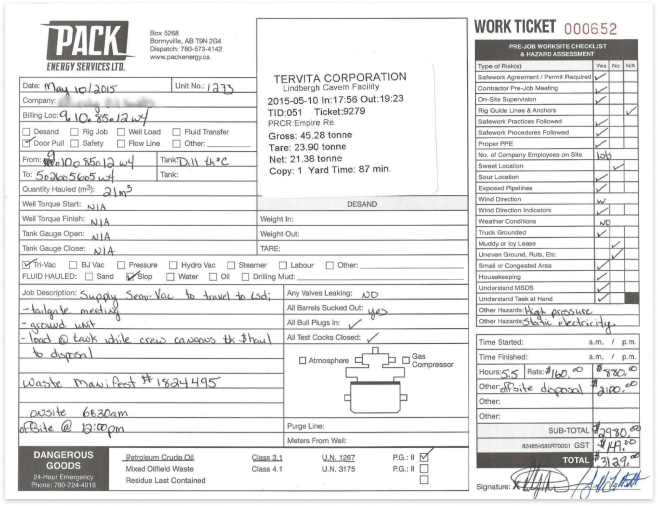
Tickets are a source of truth for key fluid hauling business data including pickup location, destination, fluid type, and volume. We became all too familiar with the inefficiencies related to paper-based fluid tracking and ticketing.
What are the pain points with paper-based truck ticketing?
Paper tickets put a significant burden on admins for both the oil company (i.e. field operators, production accounting teams, accounts payable) and their service providers (i.e. accounts receivable). Here are the pain points:
- Data is not real-time, as there is a significant delay between creation of the ticket to when it gets entered into production data software.
- It is labor-intensive and error-prone to manually transfer paper ticket data into a production data software.
- Data quality issues arise when planned volumes are different than what actually got hauled, or when planned destination is different than where the fluid was actually hauled.
- Manual reconciliation of paper tickets with production data software, disposal facility invoices, or trucking company invoices is a burden for admins. Time is wasted writing up tickets, driving around to get them approved, and driving around to collect from the various locations they are dropped at.
- Time is wasted writing up tickets, driving around to get them approved, and driving around to collect from the various locations they are dropped at.
How can IronSight revolutionize fluid hauling and digitize truck tickets?
Request
Mobile app
The first step is to create the fluid haul job in IronSight. Typically a job is requested by a field operator or dispatcher using IronSight’s mobile or web apps. If you can order pizza using a mobile phone app you can also use IronSight. Why? We are obsessive about user experience, and our request wizard exemplifies how easy it can be to get your field team to capture key fluid haul data, including:
- Fluid type
- Volume
- Pickup Location
- Destination Location
- Date and Times
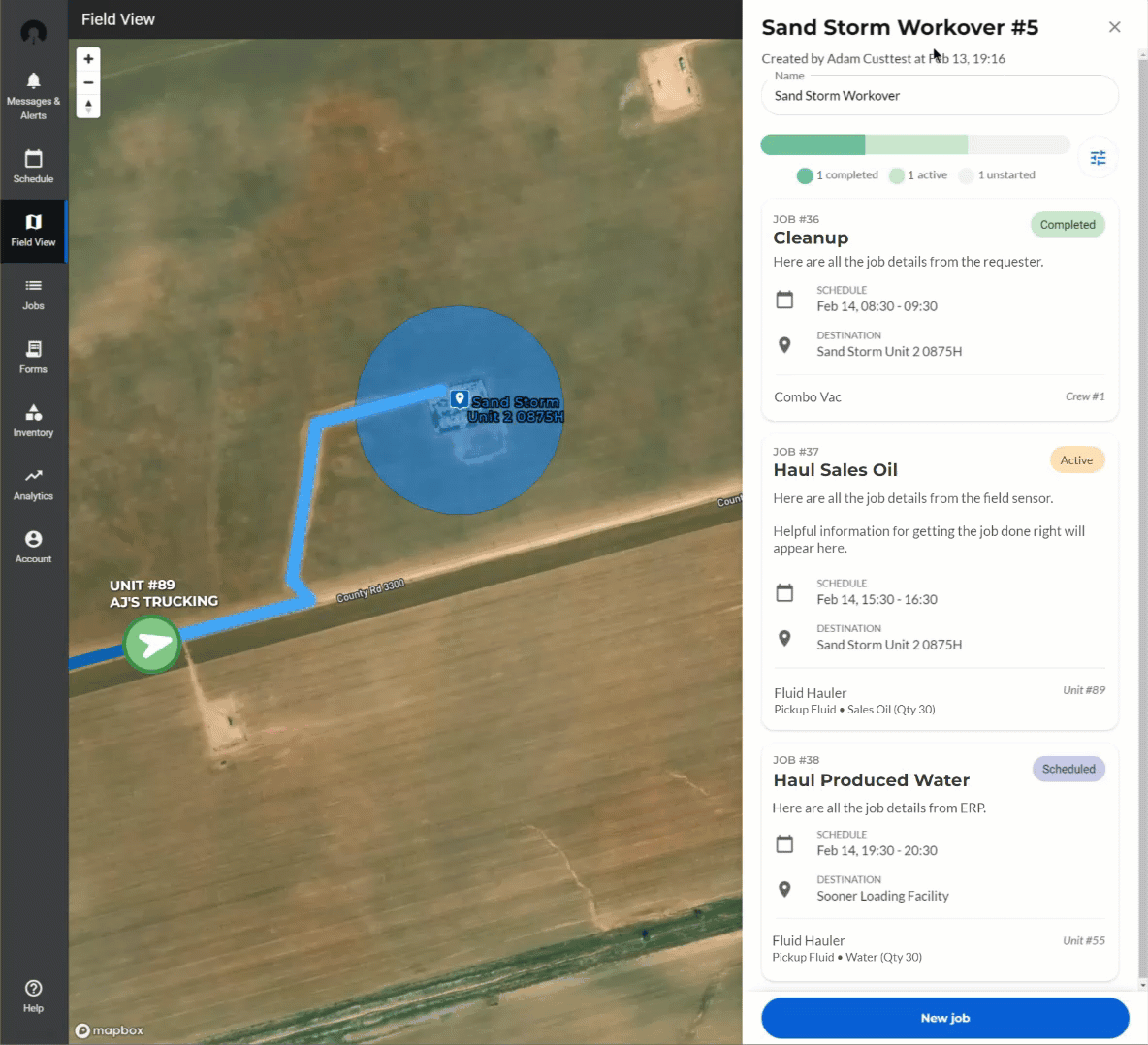
AUTOMATED REQUEST/DISPATCH (FROM SCADA OR ERP)
Integrate your field sensors, SCADA, and/or your enterprise software (ERP / CMMS / EAM) to automatically request and dispatch jobs in IronSight.
Schedule
Coordinators have a real-time, birds-eye view of their entire operation. All they need to do is drag-and-drop to dispatch the job to the optimal fluid hauler.
ADVANCED FEATURES AVAILABLE
Coordinators have a real-time, birds-eye view of their entire operation. All they need to do is drag-and-drop to dispatch the job to the optimal fluid hauler.
- Ensure you assigning the optimal service provider with Dynamic Dispatch, our auto-dispatch feature
- Group related jobs into projects
- Use recurring jobs to create loads that happen on a routine schedule
.gif)
Execute & Document
Coordinators have a real-time, birds-eye view of their entire operation. All they need to do is drag-and-drop to dispatch the job to the optimal fluid hauler.
DRIVERS BENEFIT FROM
- fully detailed work list
- notifications for new jobs and updates
- driving directionse
- elimination of paperwork
.gif)
Approve
The oil company can review/edit the locations, times, and volumes on a completed job. If everything looks valid, they press approve and the data is automatically sent into production accounting and invoicing systems, no paper tickets required.
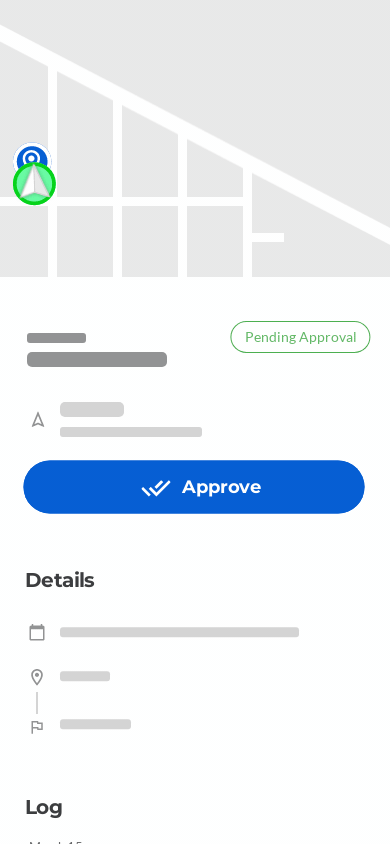
Integrate & Analyze
Coordinators have a real-time, birds-eye view of their entire operation. All they need to do is drag-and-drop to dispatch the job to the optimal fluid hauler.
DASHBOARDS
Throughout the entire fluid haul, IronSight’s apps are collecting vast amounts of field data which can be analyzed in real-time dashboards. You can immediately spot opportunities to increase the utilization of your resources, which translates into getting more work done (including catching up your backlog) and lowering annual operating cost.
.gif)
INTEGRATIONS
Save your team from hundreds of hours of data entry every month. Integrations with leading production accounting and invoicing systems eliminate lengthy approval and verification processes.
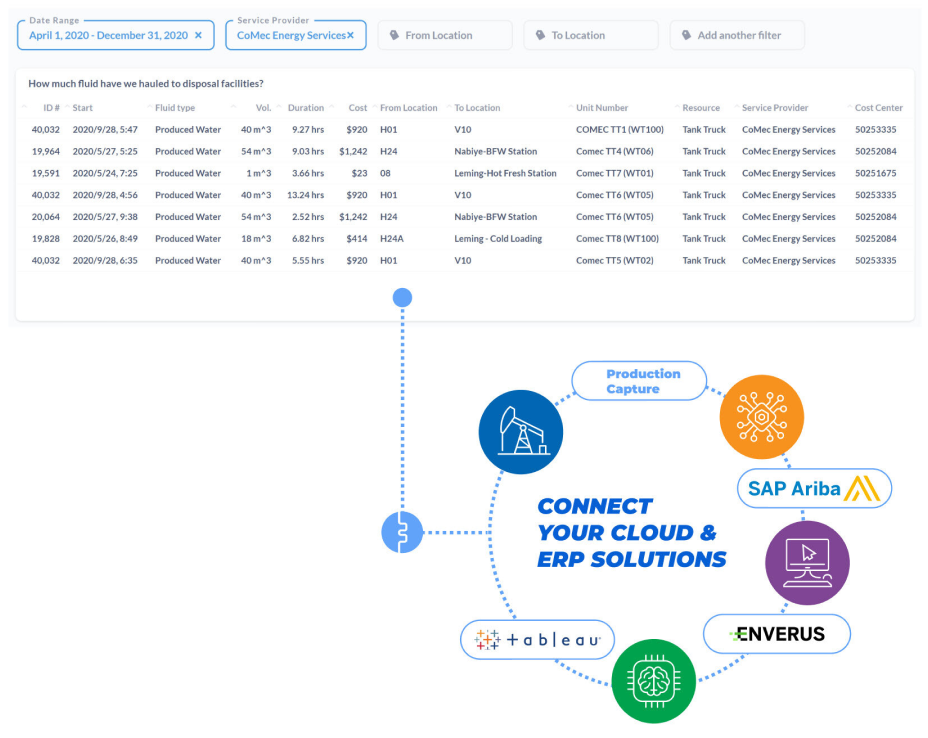
Integrations
IronSight integrates seamlessly with your existing software to take the gruntwork out of field operations.
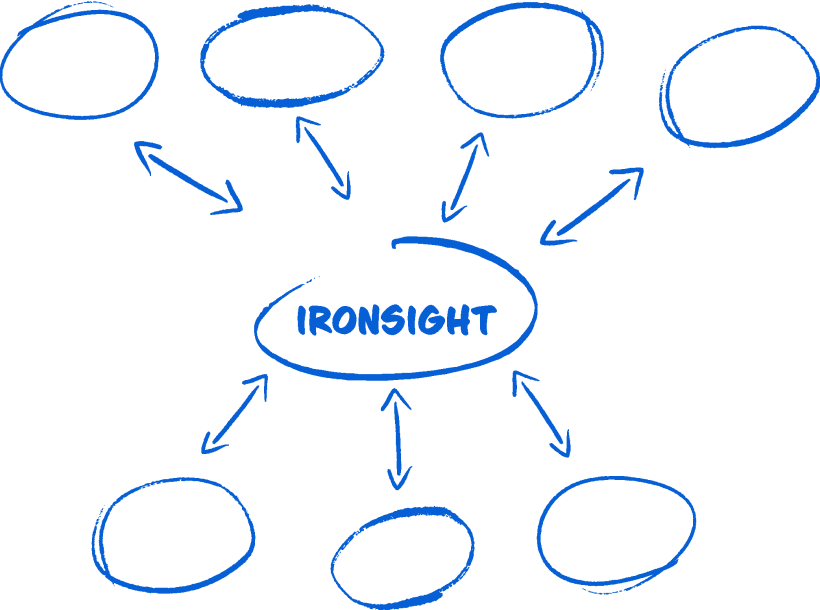